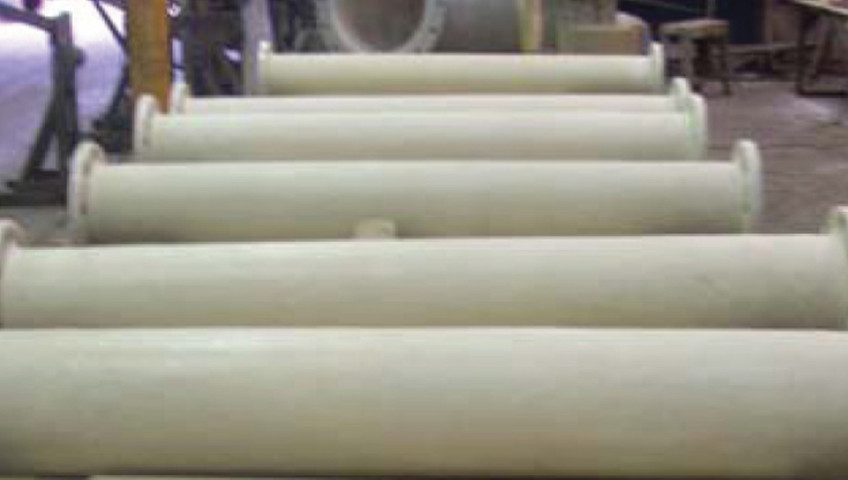
Corroglass 600 for riser pipes
Seawater pump riser pipes maintained after 21 years.
Scope of work
Maintenance work to clean, inspect, touch up minor mechanical damage externally, and recoat flange areas.
Products
Polyglass Standard for original coating in 1983
Corroglass 600 Series for repair work in 2004
Substrate
Steel
Coating system
Flash blast the existing coating. Grit blast damaged flange areas to ISO 8501-1, cleanliness standard SA 2 1/2 with minimum surface profile of 50μm. Apply Corroglass 600 Series to a min.dft of 1.5mm. Thickness check and spark test to 19Kv Hv-AC.
Coating credentials
These seawater pump riser pipes first came to Corrocoat 21 years ago, and were protected internally and externally with the original Polyglass Standard product. During the service life, which comprised external exposure to seawater (immersed, splash zone and atmospheric), and internally, seawater with a low hydrochlorite dosing (4%), the coating has not shown any tendency to undercut, and only minor mechanical damage was needed to be repaired. The sustained performance of Polyglass Standard under adverse operating conditions demonstrates the products’ suitability for use in diverse applications throughout industry.
Photographs
The pipes as returned after 21 years’ service
Flange area illustrating no under-cutting
Pipes in coating – almost complete
Seawater pump riser pipes maintained after 21 years.
Scope of work
Maintenance work to clean, inspect, touch up minor mechanical damage externally, and recoat flange areas.
Products
Polyglass Standard for original coating in 1983
Corroglass 600 Series for repair work in 2004
Substrate
Steel
Coating system
Flash blast the existing coating. Grit blast damaged flange areas to ISO 8501-1, cleanliness standard SA 2 1/2 with minimum surface profile of 50μm. Apply Corroglass 600 Series to a min.dft of 1.5mm. Thickness check and spark test to 19Kv Hv-AC.
Coating credentials
These seawater pump riser pipes first came to Corrocoat 21 years ago, and were protected internally and externally with the original Polyglass Standard product. During the service life, which comprised external exposure to seawater (immersed, splash zone and atmospheric), and internally, seawater with a low hydrochlorite dosing (4%), the coating has not shown any tendency to undercut, and only minor mechanical damage was needed to be repaired. The sustained performance of Polyglass Standard under adverse operating conditions demonstrates the products’ suitability for use in diverse applications throughout industry.
Photographs
The pipes as returned after 21 years’ service
Flange area illustrating no under-cutting
Pipes in coating – almost complete
Recent Comments