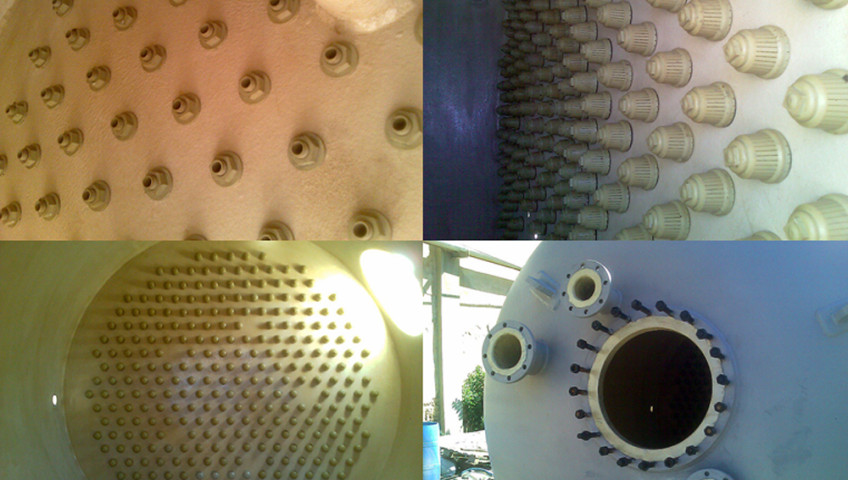
Refurbishment of Cation Exchanger Regeneration
Refurbishment and protection for petrochemical industry.
Scope of work
Complete refurbishment of process vessel currently out of service facing fatal corrosion problems. Previous hard rubber coating failed with lot of undercorroded areas.
Products
POLYGLASS Range
PLASMET ZF
Substrate
Carbon steel
Application Method
After taking down current hard ruber and 3 badly corroded parts rewelded, internal of the vessel protected against Sulphuric Acid 15% concentration attack at 60°C temperature, pressure 5 bars, using CORROCOAT materials: primer PPA, Polyglass Pipe Grade for 296 vertical hole of nozzle plate (hot spot of job), Corrofill, Polyglass VEF, Polyglass Veil Coat. Postcured. External protected by Plasmet ZF.
Coating credentials
The success of this project has led to the customer specifying Corrocoat systems to protect other areas of petrochemical plant including high aggressive chemical and temperature attack areas.
Photographs
Previous hard rubber coating
Spray application of Polyglass VEF
Process vessel after refurbishment
Refurbishment and protection for petrochemical industry.
Scope of work
Complete refurbishment of process vessel currently out of service facing fatal corrosion problems. Previous hard rubber coating failed with lot of undercorroded areas.
Products
POLYGLASS Range
PLASMET ZF
Substrate
Carbon steel
Application Method
After taking down current hard ruber and 3 badly corroded parts rewelded, internal of the vessel protected against Sulphuric Acid 15% concentration attack at 60°C temperature, pressure 5 bars, using CORROCOAT materials: primer PPA, Polyglass Pipe Grade for 296 vertical hole of nozzle plate (hot spot of job), Corrofill, Polyglass VEF, Polyglass Veil Coat. Postcured. External protected by Plasmet ZF.
Coating credentials
The success of this project has led to the customer specifying Corrocoat systems to protect other areas of petrochemical plant including high aggressive chemical and temperature attack areas.
Photographs
Previous hard rubber coating
Spray application of Polyglass VEF
Process vessel after refurbishment
Recent Comments