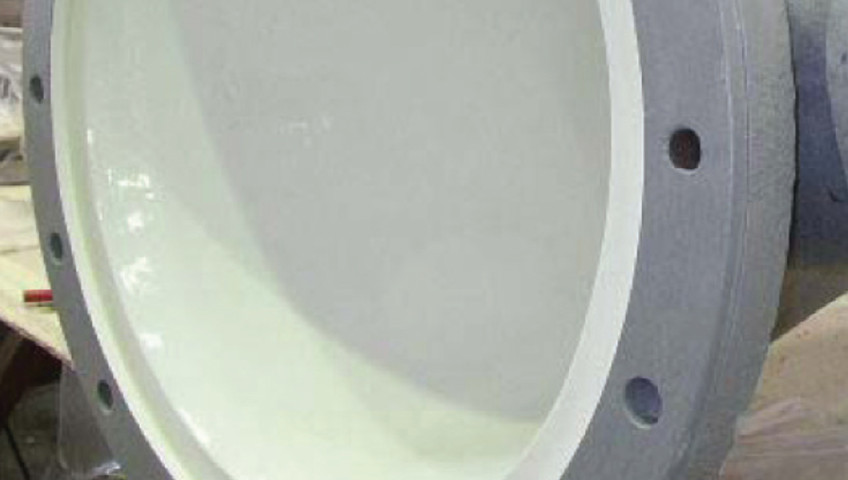
Corrocoat ‘E’ series for a venturi
Long term corrosion protection for venturi.
Scope of work
Refurbish and protect a venturi from a sea-water, condensate water system. The component illustrated cavitation and undercutting damage, with severe corrosion around the flange area.
Products
Corrocoat EA/EB, Fluiglide E & Plasmet ZF
Substrate
Cast iron
Coating system
Grit blasted internally to ISO 8501-1 cleanliness standard SA 2 1/2. Grit blasted externally to ISO 8501-1 cleanliness standard SA 2. Applied internally Corrocoat EA / EB to achieve a minimum dft of 2.0mm followed by a top coat of Fluiglide E. Applied externally 2 coats of Plasmet ZF followed by a cosmetic top coat.
Coating credentials
Corrocoat’s EA and EB series provide a high build flexibilised epoxy system with good resistance to erosion, cavitation and impact, when used at thicknesses above 1.5mm. Originally these components were glass lined. Corrocoat can either repair, or completely refurbish Glass lined components – depending on the level of damage, and the environment in which they are operating. The use of glass-flake linings, specially manufactured for their cavitation, erosion and impact resistance offers an excellent alternative to glass and other linings – subject to the environmental conditions being within the specification of the glass-flake lining. Glass frit lining can be expensive and time consuming due to the subsequent stoving required. The additional process steps required in glass frit lining also negates the possibility of on site application or repair if required. Glassflake linings can be applied and repaired on site.
Photographs
The venturi on arrival in our Leeds works
Severe undercutting & cavitation damage in the flange area
Completed repair and refurbishment and awaiting packing and despatch to customer
Long term corrosion protection for venturi.
Scope of work
Refurbish and protect a venturi from a sea-water, condensate water system. The component illustrated cavitation and undercutting damage, with severe corrosion around the flange area.
Products
Corrocoat EA/EB, Fluiglide E & Plasmet ZF
Substrate
Cast iron
Coating system
Grit blasted internally to ISO 8501-1 cleanliness standard SA 2 1/2. Grit blasted externally to ISO 8501-1 cleanliness standard SA 2. Applied internally Corrocoat EA / EB to achieve a minimum dft of 2.0mm followed by a top coat of Fluiglide E. Applied externally 2 coats of Plasmet ZF followed by a cosmetic top coat.
Coating credentials
Corrocoat’s EA and EB series provide a high build flexibilised epoxy system with good resistance to erosion, cavitation and impact, when used at thicknesses above 1.5mm. Originally these components were glass lined. Corrocoat can either repair, or completely refurbish Glass lined components – depending on the level of damage, and the environment in which they are operating. The use of glass-flake linings, specially manufactured for their cavitation, erosion and impact resistance offers an excellent alternative to glass and other linings – subject to the environmental conditions being within the specification of the glass-flake lining. Glass frit lining can be expensive and time consuming due to the subsequent stoving required. The additional process steps required in glass frit lining also negates the possibility of on site application or repair if required. Glassflake linings can be applied and repaired on site.
Photographs
The venturi on arrival in our Leeds works
Severe undercutting & cavitation damage in the flange area
Completed repair and refurbishment and awaiting packing and despatch to customer
Recent Comments